Chapter 11 -- Setting Tool Length Offsets (TLOs)
Definition of TLO
The Tool Length Offset or TLO is the measurement (-Z axis value) that the spindle would have to move from the maximum spindle up position (e.g., Tool 0 (zero) at ABS Z=0) to a particular gage or reference surface. TLOs are the mechanism the controller, programmer, and operator account for the difference in the length of the various tools. TLOs therefore permit the programmer to write a part program independent of tool length and the operator to run programs without having to alter the workpiece's Z-axis value because of differences in tool length.
Normally, each tool will have a different TLO value--the main exceptions being when using dummy values during program development and when creating pen plots. The programmer must assume that each tool's Z axis position is set and confirmed properly by the operator. Correspondingly, the operator must set &/or confirm each TLO prior to running the program.
Setting TLOs is done by touching each tool off from a feeler gage (for example, a 0.100" gage block) set on some reference or Z-datum surface (e.g., the top surface of the secured workpiece or the top surface of a mounting plate the workpiece sets on). After installing the tool in the spindle, the operator "jogs" the Z axis until the tip of the tool just barely touches the gage surface. The length of the jog move is thus the TLO and will be stored in one of the controller's 32 TLO registers.
Whenever a tool change command (a tool number such as T2) is acted upon, the Crusader II controller will access tool register #2 (that is the memory location associated with tool #2) and shift the Z-axis origin so it is has a Z-axis value of zero (0) when the tool tip is right at the gage surface.
Programming T0 (pronounced "tool zero") will cancel any active TLO and return the Z-zero reading to its absolute location. The T0 command does not retract the quill. To retract the quill, the T0 command must be followed by a rapid travel, absolute coordinate Z0 (T0 G00 G90 Z0).
NOTE:
It is the operator's responsibilty to
set &/or confirm the accuracy of all TLOs. |
Procedure for Setting TLOs (Manually Programming the Anilam Controller)
Setting TLOs is sometimes referred to a "zeroing the tools". The procedure is as follows:
- Assign a tool number to each tool as determined in the program (usually in the order of use).
- After the program has been loaded, make sure the first section of the program has provision for entering the TLO values. If missing, insert the necessary blocks to make the program appear as follows:
EVENT
1 TOOL 1001
2 BLANK BLOCK
3 TOOL 1002
4 BLANK BLOCK
5 TOOL 1003
6 BLANK BLOCK
ETC.
- Mount each tool into its own tool holder.
- Press
to deactivate any TLO that may be in effect.
- Retract the quill by pressing

- Raise or lower the knee to a position that will
(a) permit the longest tool to be installed with the quill fully retracted
and
(b) permit the shortest tool to be used without causing quill motion that will hit the limit switch.
- Install the first desired tool (e.g., Tool #1) in the spindle.
- Place the feeler gage on the Z-axis reference surface.
- In order to transfer the value of the jog distance from the display to the TLO register (true digitizing), perform the following steps:
- Place the controller in Manual mode

- Carefully jog the tool down
until it just barely touches the feeler gage.
Including the thickness of the feeler gage, write down the length of the jog move for that particular tool.
- Activate the
by pressing the button as required.
The MANUAL button will remain lit (i.e.,
).
- Press the number(s) representing the event number where the TLO value is to be entered (e.g., '2') and
.
- Press the
button.
- Press
and the
button. This will enter the displayed Z-axis position into the TLO register.
- Use the
jog button to raise the cutter far enough to remove the tool.
- As required, install another tool, jog the cutter down to touch off on the feeler gage, and repeat the steps B-G.`
Alternate (Faster) Procedure for Setting TLOs (Manually Programming the Anilam Controller)
A simpler method to enter TLO values onto their appropriate registers when manually programming the controller is shown in the following steps:
- Determine the (negative) Z-axis value of each TLO as follows:
- Place the controller in Manual mode

- Carefully jog the tool down
until it just barely
touches the feeler gage.
Including the thickness of the feeler gage, write down the length of the jog move for that particular tool.
- Return the quill to the fully retracted position by pressing
.
- Repeat the Steps B & C for the remaining tools, writing down their jog lengths.
- Input the appropriate Z-axis value of each TLO into the controller's memory as follows:
- Press
to deactivate the axes position display.
- Press
to call up the first blank block reserved for tool 1's TLO.
- Press
and then Tool 1's jog value followed by
.
- Repeat Steps B & C to enter the TLO jog values for tools 2, 3, 4, etc.
Note that the memory locations for the subsequent TLOs will will be stored in events 4, 6, 8, etc.
- Retract the quill and verify the accuracy of the TLO data by pressing
, etc.
Procedure for Setting TLOs When Programming Off-Line (EIA-274 Format)
Sequence of events:
- Develop the program with "dummy" TLO values for each tool used.
Note: A comment above the TLO definitions &/or in set-up instructions
will alert an operator to required action regarding setting or confirming TLOs.
Example EIA-274 Formatted Code with Dummy TLO Values
N0010 G00 G90 G70 $ RPD ABS INCH
$ --------------------------------------------------
$ TLOs _MUST_ be set by operator _PRIOR_ to program run
$ --------------------------------------------------
N0021 G29 T1001 Z-2 $ TLO Tool #1
N0022 G29 T1002 Z-2 $ TLO Tool #2
N0023 G29 T1003 Z-2 $ TLO Tool #3
etc.
- Determine the TLO of each tool using Step #1 of the Alternate Procedures for setting TLOs above.
- Then, either
- After transferring the program into the controller's memory, insert the appropriate TLO values
directly into program memory using Step #2 of the Alternate Procedures above;
or
- Before transferring the program from the PC to the Controller, place the appropriate TLO values directly into the CNC program.
Example EIA-274 Formatted Code with Actual TLO Values
Note the Date, Time, & Operator stamp.
N0010 G00 G90 G70 $ RPD ABS INCH
$ --------------------------------------------------
$ TLOs set Feb. 11, 2003 by James Bigglesly
$ --------------------------------------------------
N0021 G29 T1001 Z-1.932 $ TLO Tool #1
N0022 G29 T1002 Z-2.302 $ TLO Tool #2
N0023 G29 T1003 Z-2.700 $ TLO Tool #3
etc.
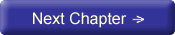
Copyright © 2003 George C. Stanton & Bill Hemphill
All Rights Reserved
Last updated on Feb. 8, 2003 by Bill Hemphill