Bridgeport
Heidenhain CNC Mill
Programming & Operating Instructions
Chapter 4
Canned Cycles
Drilling (called "Pecking")
Preliminary information
When activated by a G79 command, the cutter will feed down a specified "peck"
distance (which could be equal to the entire hole depth) at a specified downfeed rate. The
cuter will then rapid travel out of the hole to clear the chips and then (if a second,
etc. peck is required) rapid back down almost to the bottom of the hole and then feed down
another peck increment. The process is repeated until the final depth is achieved. A dwell
can be specified for countersinking, spotfacing, and counterboring operations.
ISO format syntax and parameter values
Nxxx G83 P01 0 P02 -n P03 -n P04 n P05 n
where
P01 = Unneeded "clearance" parameter; set at zero (0)
- This parameter serves no useful purpose and can mess things up when improper values are
used. Simply set this parameter to zero value.
- FYI: According to the Heidenhain manual, the "SET-UP
CLEARANCE" represents the distance above the top of the hole that the drill point
will be located at the beginning of the cycle. In effect this tells the controller the incremental
distance from the tool point to the surface to be drilled (typically set at 0.100 inch). Therefore
this value must be assigned a negative ( - ) sign! Be sure to have the drill
located at this Z-plane when activating (calling up) the cycle.
P02 = TOTAL Z-STROKE (Incremental; MUST be negative!)
P03 = Peck increment (set @ P02 value for no peck)
P04 = Dwell (sec) Set at zero.
P05 = Drill feedrate (IPM; format = 2.1; decimal assumed, not entered.)
Activate the drill cycle with:
Nxxx G79 M03
The "G79" activates the drill cycle. The "M03" is required to activate the spindle (even though it is already turning).

Rectangular Pocket Milling
Preliminary information
This cycle assumes the cutter is initially placed over the center of the pocket and at
some clearance distance (typically 0.100 inch) above the top of the pocket. Then the cycle
will take over from that point, plunging the cutter down to the "peck depth" and
feeding the cutter around the pocket in ever increasing increments until the final size is
attained. The process is repeated until the desired total depth is attained. Then the
cutter is returned to the center of the pocket at the clearance height.
The overall length and width of the pocket, rather than the distance of cutter motion,
are programmed into this cycle. The controller must be told what the cutter
radius is in the tool definitation statement.
The amount of stepover for each go-around of the cutter is calculated by the controller
and cannot be specified by the programmer.
Use this cycle for rouging out pockets. There is no provision for a light finish pass
for the final go-around. Likewise, there is no provision for corner radii (other than the
cutter's radius), nor for a downfeed ramp. Hence it is wise to leave the
pocket undersize, and then program individual axis moves to finish the pocket.
ISO format programming syntax and parameter values
for the G75 (CW) & G76 (CCW) Rectangular Pocket Cycles.
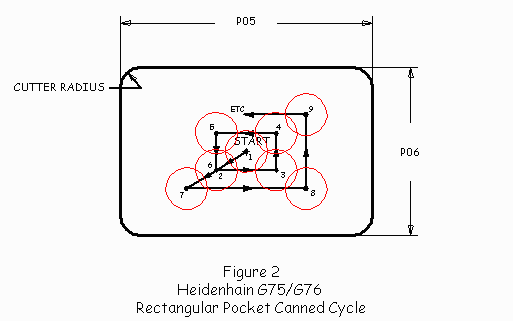
Syntax:
G75 P01 0 P02 -n P03 -n P04 n P05 X+n P06 Y+n P07 n
or
G76 P01 0 P02 -n P03 -n P04 n P05 X+n P06 Y+n P07 n
where:
P01 = Unneeded "clearance" parameter; set at zero
- This parameter serves no useful purpose and can mess things up when improper values are
used. Simply set this parameter to zero value.
- FYI: According to the Heidenhain manual, the "SET-UP CLEARANCE"
represents the distance above the top of the hole that the tool point will be located at
the beginning of the cycle. In effect this tells the controller the incremental
distance from the tool point to the surface to be drilled (typically set at 0.100 inch). Therefore
this value must be assigned a negative ( - ) sign! Be sure to have the
drill located at this Z-plane when activating (calling up) the cycle.
P02 = Pocket depth (incremental; must be negative)
P03 = Peck increment (set at P02 value for no peck)
P04 = Downfeed feedrate
P05 = 1st (longer) side axis & length
P06 = 2nd (shorter) side axis & length
P07 = X/Y feedrate

Circular Pocket Milling
Preliminary information
This cycle assumes the cutter is initially placed over the center of the pocket and at
some clearance distance (typically 0.100 inch) above the top of the pocket. Then the cycle
will take over from that point, plunging the cutter down to the "peck depth" and
feeding the cutter around the pocket in a spiral path until the final size is attained.
The process is repeated until the desired total depth is attained. Then the cutter is
returned to the center of the pocket at the clearance height.
The overall radius of the pocket, rather than the radius of cutter motion, is
programmed into this cycle. The controller must be told what the cutter
radius is in the tool definitation statement.
The amount of stepover for each go-around of the cutter is calculated by the controller
and cannot be specified by the programmer.
There is no provision for a downfeed ramp nor for a light finish pass for the final
go-around. It is wise to use this cycle for roughing out purposes, leaving the
pocket undersize, and then program a separate circular interpolation statement to finish
the pocket.
ISO format programming syntax and parameter values
for the G77 (CW) & G78 (CCW) Circular Pocket Cycles
G77 P01 0 P02 -n P03 -n P04 n P05 n P06 n
or
G78 P01 0 P02 -n P03 -n P04 n P05 n P06 n
where
P01 = Unneeded "clearance" parameter; set at zero
- This parameter serves no useful purpose and can mess things up when improper values are
used. Simply set this parameter to zero value.
- According to the Heidenhain manual, the "SET-UP CLEARANCE" represents the
distance above the top of the hole that the tool point will be located at the beginning of
the cycle. In effect this tells the controller the incremental distance from the tool
point to the surface to be drilled (typically set at 0.100 inch). HENCE THIS VALUE MUST BE
ASSIGNED A NEGATIVE (-) SIGN! Be sure to have the drill located at this Z-plane when
activating (calling up) the cycle.
P02 = Pocket depth (incremental; must be negative)
P03 = Peck increment (set at P02 value for no peck)
P04 = Downfeed feedrate
P05 = Pocket radius
P06 = X/Y feedrate

Datum (Origin) Shift
Preliminary information
- This cycle is active immediately upon definition.
- Datum shift can be specified in either absolute (default) or incremental terms.
- One, two, or all three axes can be "shifted" in a single statement.
ISO format programming syntax and parameter values
G54 G90 Xn.nnn G90 Yn.nnn G90 Zn.nnn
or
G54 G91 Xn.nnn G91 Yn.nnn G91 Zn.nnn
where
G90 = Origin shift to absolute current location
G91 = Origin shift to incremental location
- Omit axes with no change
- Incremental and absolute can be mixed.

Mirror Image
Preliminary information.
- This cycle is active immediately upon definition.
- Mirroring always occurs about the origin; it may be necessary to shift the origin to a
new location in order to have the mirror axis in the desired location.
- Mirroring can occur about the X axis, Y axis, or both the X and Y axes.
ISO format programming syntax and parameter values
for the G77 (CW) & G78 (CCW) Circular Pocket Cycles
G28 [axis to be mirrored about] (e.g., G28 X)

Rotation
Preliminary information.
- This cycle rotates the coordinate system a specified number of degrees, either
incrementally, or absolute relative to angle zero at the 3:00 o'clock position.
- This cycle is active immediately upon definition.
- Rotation always occurs about the origin; it may be necessary to shift the origin to a
new location in order to have the axis of rotation at the desired location.
ISO format programming syntax and parameter values
G90 G73 H+nnn G17
H-nnn G18
G19
where
H+nnn = Counterclockwise rotation angle
H-nnn = Clockwise rotation angle
G17 = Rotation of the X-Y plane (usual choice)
G18 = Rotation of the X-Z plane
G19 = Rotation of the Y-Z plane

SCALING
Preliminary information
- This cycle multiplies all coordinates and radii by the specified factor. It does NOT
move the origin.
- This cycle is active immediately upon definition.
ISO format programming syntax and parameters
G72 Fn.nnn
where
F = Scaling factor (0 to 99.999999)
Scaling is canceled by redefining a G72 cycle and specifying
a scaling factor of zero. It is also canceled by the M30 at the end of a program.

|