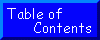
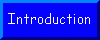 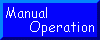
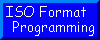
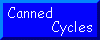
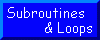
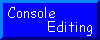
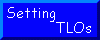
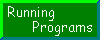




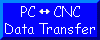
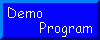
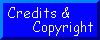
|
Bridgeport
Heidenhain CNC Mill
Programming & Operating Instructions
Chapter 8
Running Programs
Transfering programs into the "run" buffer
- Press the program run-continuous
key.
- Press the Program Number
key to display the directory of programs resident in the controller's memory.
- Choose the program you wish to run by either using the cursor keys or by entering the
number of the program using the numeric key pad. Press the Enter
key.

Dry running programs
- Press the Dry Run
key to
check out program for syntax errors, math errors, and axis limit interferences without
actually moving and axes.
The program will run until an error, a dwell, or a tool change command is encountered.
- When a dwell (G38) or tool change is encountered, press the NO ENT
key to cause the program to
continue its run.
- When a syntax or programming error is encountered, an error message will be displayed.
Most messages are self-explanatory. If you don't understand the
message, refer to the error message section of the Heidenhain Operating Manual.
- Ultimately, if no errors are encountered, the CRT will redisplay the first block of the
program.

Going for broke
- Clean, stone, and wipe down the table.
- Clean, stone, and wipe down the vise, quick mount base plate, or workpiece thoroughly.
- Mount the vise, quick mount base or workpiece on the table and clamp securely.
- Indicate in the vise's fixed jaw or the quick mount base plate to within 0.001"
runout.
- If using the quick mount system, clean, stone (as appropriate), and wipe down the
carrier (top) plate. Secure the carrier plate to the base plate using two ball
locks. Tighten the Allen screws securely.
- If this is not a production run of a proven part (i.e., it is a test of a student
generated program), do not install any cutters into the spindle.
- Note where all clamps, if used, are located. Make
sure the program will not send the cutter into the clamps. If
necessary, relocate the clamps or modify the program.
- "Float" the X-Y origin to the desired location
using an edge finder or dial indicator as described in Chapter 2.
- Mount the cutters in their holders and set the tool length
offsets as described in Chapter 7.

Precautions
Run the program through
without cutters installed to see if it looks like everything is going where its supposed
to go.
- The first time through use the single block mode. Press the RUN SINGLE BLOCK
key.
- Second time through use the continuous run mode. Press the RUN CONTINUOUS
key.
- Note the dial reading on the knee dial. Drop the knee down a sufficient distance so that
no cutter will contact the workpiece. Record the distance. Then run the program through in
the continuous or single-block mode as you choose. If everything looks OK, then raise the
knee back to its former position.
- It is always wise to first run a dummy part in wood or machinable waxjust in case
an error remains.
- After running the first genuine workpiece, perform a First Article
Inspection Report, measuring each dimension and comparing it to the print dimension and
tolerance. Make any necessary adjustments to the program and/or setup. Then run and check
another piecepart. Once a good part is obtained, the rest of the run will be just like it.

|